Understanding Prototype Mold Manufacturers and Their Impact on Business
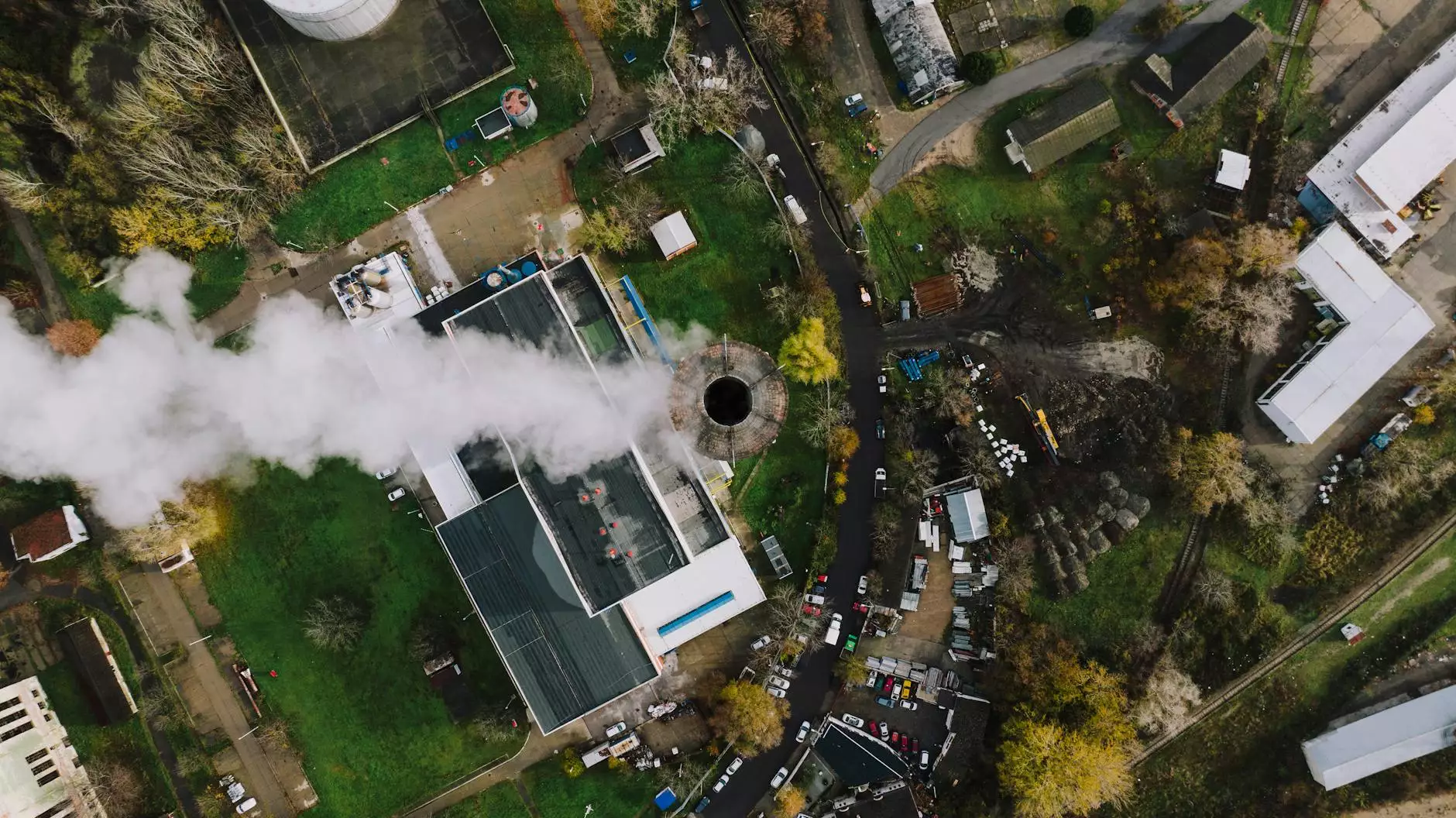
Prototype mold manufacturers play an essential role in various industries, providing critical services that drive innovation, efficiency, and competitiveness. This article delves into the processes, benefits, and significance of these manufacturers, particularly focusing on how they cater to the needs of businesses in the metal fabrication sector.
The Role of Prototype Mold Manufacturers
Prototype mold manufacturers are specialized firms that create molds for producing prototypes. These prototypes are used to test designs, materials, and functionalities prior to full-scale production. This process is crucial for several reasons:
- Cost Efficiency: Creating a prototype allows companies to identify and rectify design flaws early, saving costs associated with mass production errors.
- Rapid Prototyping: With advancements in technology, manufacturers can produce prototypes quickly, allowing for faster iterations of designs.
- Enhanced Collaboration: Prototypes enable better communication among design teams, clients, and stakeholders, ensuring everyone has a tangible product to discuss.
Importance of Prototyping in Metal Fabrication
In the realm of metal fabricators, the importance of prototyping cannot be overstated. Metal fabrication involves the design and manufacture of metal structures, and having a prototype can streamline this process dramatically. Here’s why prototyping is pivotal in metal fabrication:
- Material Testing: Different metals and alloys react differently under stress and heat. Prototypes allow manufacturers to test these materials under realistic conditions.
- Design Validation: Functional testing of a prototype can reveal insights into the design's effectiveness, ensuring that the final product meets necessary specifications.
- Faster Time to Market: By using prototypes, metal fabricators can significantly reduce the time it takes to finalize a design and move into production.
Types of Prototype Molds
There are several types of molds used by prototype mold manufacturers, each serving distinct purposes in the prototyping process:
1. Injection Molds
Injection molds are widely used for creating intricate parts and components. They involve injecting molten material into a mold cavity, where it cools and solidifies into the desired shape. This method is efficient for high-volume production.
2. Blow Molds
Blow molds are utilized for making hollow parts, particularly in industries like packaging. The process involves inflating a heated plastic tube inside a mold, forming the shape of a container or hollow product.
3. Compression Molds
Compression molding is ideal for producing rubber and thermoplastic parts. The raw material is placed into a heated mold and compressed, allowing it to take on the shape of the mold cavity.
4. 3D Printed Molds
Advancements in 3D printing technology have enabled manufacturers to create molds quickly and cost-effectively. This method is particularly beneficial for low-volume production and rapid prototyping.
Choosing the Right Prototype Mold Manufacturer
When selecting a prototype mold manufacturer, businesses should consider several key factors to ensure that their needs are met effectively:
- Experience and Expertise: Look for manufacturers with a proven track record in producing molds for products similar to what your company needs.
- Technology Utilization: Evaluate the technology used by the manufacturer. Advanced machinery and software can significantly enhance accuracy and efficiency.
- Material Options: A good manufacturer should offer a wide range of material choices to suit different project requirements.
- Quality Assurance: Ensure that the manufacturer has a robust quality control process in place to maintain high standards throughout the production process.
Benefits of Collaborating with Prototype Mold Manufacturers
Collaborating with prototype mold manufacturers can yield significant advantages for businesses, including:
- Increased Innovation: By providing a platform for testing new ideas and designs, these manufacturers foster innovation.
- Tailored Solutions: Manufacturers can customize molds based on specific business requirements, ensuring higher satisfaction with the final product.
- Technical Support: Many manufacturers offer technical support throughout the design and production process, guiding companies through challenges and offering expert advice.
- Market Adaptability: Quick prototyping allows businesses to adapt to market demands swiftly, staying ahead of the competition.
Case Studies: Successful Businesses Leveraging Prototype Molds
To illustrate the impact of prototype mold manufacturers, let's explore a few case studies of businesses that have successfully utilized prototyping in their operations:
Case Study 1: Automotive Industry
A leading automotive manufacturer faced challenges in developing a new lightweight component for their vehicles. By collaborating with a prototype mold manufacturer, they produced several designs for testing. The rapid iteration process allowed them to refine their designs based on comprehensive performance data, ultimately leading to a more efficient manufacturing process and a competitive edge in the market.
Case Study 2: Consumer Electronics
A consumer electronics company needed a new casing design for a product launch. By utilizing 3D printed molds, they were able to create multiple prototypes in a fraction of the time compared to traditional methods. This not only saved time but also allowed them to receive feedback from focus groups early in the design phase, leading to a more market-friendly product.
Case Study 3: Medical Devices
A company specializing in medical devices required a prototype for a new surgical instrument. The use of compression molds allowed them to create durable prototypes that underwent rigorous testing for safety and efficacy. The insights gained allowed for enhancements before entering mass production, ensuring compliance with medical industry standards.
Conclusion: The Future of Prototype Mold Manufacturing
As industries continue to evolve and demand for customized solutions rises, the role of prototype mold manufacturers will only become more critical. Companies like deepmould.net are at the forefront, offering innovative solutions that meet the dynamic needs of various sectors. Embracing advancements in technology, these manufacturers will further enhance the prototyping process, paving the way for future innovations.
Investing in quality prototyping is not merely a trend; it is an essential strategy for businesses aiming to succeed in today’s competitive landscape. The collaboration with skilled prototype mold manufacturers can facilitate innovation, reduce costs, and ultimately lead to products that stand out in the marketplace.